Is it a screw? A rivet? Why not both.
I found this dud in a bag of screws.
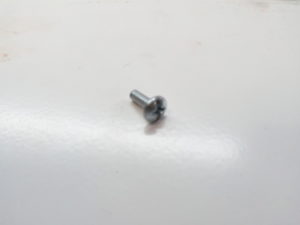
Is it a screw? A rivet? Why not both.
I found this dud in a bag of screws.
After spending a great part of the other day refurbishing a nice chuck I set out to fix some of the problems on the drill press.
The whole quill tube has a lot of play but turns out there’s a set screw loose that just makes it better.
I chucked a short section of precision ground bar and set up a dial indicator while I ran the pulley with my hand. The run out was around two tenths of millimeter. Tried again after moving the jaws and applying more force but the result was the same.
Some fumbling and a big hit with a punch removed the chuck from the shaft. There were some patches of light corrosion on both surfaces.
Even so, a dial indicator on the drive shaft showed a wobble of a couple of hundredths. That’s more than good for a machine like this.
But looking closer inside the chuck the taper it had machining marks, like concentric ridges. I didn’t know better when I first assembled it and assumed they were for improved grip or something.
I started the motor and lightly kissed the shaft with fine sandpaper, first 800 and then some 1200 grit until it was smooth to the touch.
Then I painted it with a sharpie and installed the chuck again. This time I noticed it was kind of a loose fit and sure enough when pulling it down only some parts were inked.
I held a drill on the vise and with a paperclip and progressively fine sand paper removed the roughness inside the cone. Now there are ink spots more or less evenly distributed and the indicator registered about 15 hundredths.
Long time ago I was waiting for my turn to use the weighting scale on a scrapyard when I stepped over something curious.
Inside a sturdy chunk of mud there were the remains of an electric drill but what got my attention was the keyless chuck. I asked at the counter and got it for free.
It slept for some time on a shelf until I found it again cleaning. It resisted a civilized dismantling intent so I bathed it overnight in a mix of gasoline and paint thinner.
The front came out easily and looked good enough given it’s history except for a couple of spots with tool wounds and corrosion with significant missing iron. Seems it had been passivated on the inside.
There’s a two hole pig nut on the back and that one gave more trouble. I first tried with a round nose pliers and then a punch but it only made things worse.
I used a heat gun to clear any remnant of gasoline, hoping that it would loose the threads but no cigar. So I welded a piece of scrap and with that I managed to pry it.
Compared to the rest this part looked much better. I expected a ball bearing but there was only a hardened steel ring instead.
I padded a couple of beads on the body and after a bit of careful grinding it’s like it never spent time buried.
Now I only have to fix the horrible amount of run-out and play of the drill press.
Long ago I won a lot of used tools at an auction. Among them there was a small two ton jack.
Overall it was in fair condition but the lever was really hard to move, so I left it with other low priority things to repair.
Upon a closer look the smaller piston was bent. I chucked it into a vise and tried to loose the nuts but they were firmly stuck.
I cleaned the base with a rag and wire brush and then welded it to a piece of iron channel. I love 6010 rods. I also learned that whatever was used as hydraulic oil catches fire with ease.
Laying on the floor with one foot on it I used a big wrench and a hammer, this time succeeding in getting it apart.
It doesn’t seem like much but this small curvature made it almost impossible to pump:
I decided against straightening because with the tools I have at hand it would be very certain that I’ll scratch the good part of it and thus completely ruining the jack. So I cut the bent parts with an angle grinder.
Just by chance the parts that were badly out of shape are almost the same length as some ground rods I have from a textile machine.
The plan goes like this: drill and tap the remains of the original piston, make the rod hole bigger and use a long bolt to hold them in place.
I used the cutouts and some small welding rods from the trash to make a new cross handle.
I’m very proud of that weld, the ripples and profile are very smooth and consistent. But I had to grind it flush.
This is before the final assembly, now I can operate it with a single finger.
In the last couple of days I finished the remaining welds on the steel support and mounted it on the wall with some percussive persuasion.
I made a couple of supports:
To hang this tray from the roof beams (I also made the mess of dust and bricks):
This weekend was a bit slow.
A couple of days ago I started to learn FreeCAD, mostly for its FEM analysis mode and to build a couple of construction plans.
I made another part of the cable trays for our comms closet. Initially I wanted to use FreeCAD for that but at the end it was faster to do a bit of trig and sketch the cuts on paper. It’s held in place with a couple of rivets. I also added a layer of pvc to shield the cables from the metal edges. Fits like a glove.
I also started to build a steel support for one of the walls. We made a big opening for cables and I’m a bit uneasy about the lack of support.
Fun with a plasma cutter follows:
Continue readingWell the remote control for our transmitter is officially finished. Today as a last detail I built a couple of name tags for the cables and a bigger plate to mount on the front panel.
They are not only for aesthetic purposes but also to keep things where they should be, as sometimes they drift apart with strangers.
I cut some pieces from a scrap lamp and used the alphabet punch on them. They certainly look better with a small touch of permanent marker.
I like how they lay on the cables. All of this gives me an old time vibe feeling.
Today I started to build the rope guides for the lightning fixture. I have some nice ground rods from a textile machine that are perfect for this.
On the evening I went to Futura and cleaned up a bit the stage, moving most of it to one place:
Then I started to install real cable trays instead of our improvised version with halves of water pipes. I need to cut a small section with a special bend to accommodate the opening on the wall.
I emptied most of the rack cabinet and installed the patchbay I built earlier. I had to drill and tap another set of holes as the power outlet interfered with the movement.
I also finished that small table:
At least for now. The next step will be adding another support for the roof frame and rollers to guide the ropes around it to unblock the light path should we want to project from there.
Today I hanged the lower frame and then attached the cable trays with a set of bespoke clamps and self tapping screws.
Today I started to replace that old wooden fixture with another one made of steel.
Our original plan was to install some cable trays to have a more industrial look.
Yesterday I assembled the frames on the floor:
Today I spent most of the afternoon drilling the wood trusses on the roof and attaching the hooks. Then came the time to lower the old frame and hang the white on those hooks.
Letting it gently go down was easy:
I used some wire to attach the new frame to the old pulleys and help me lifting it near the roof. That seemed a lot easier on the planning stage but I managed to pull it off in a couple of hours.
To end this day I wound the new rope on the pulleys. Tomorrow I’ll hang the other frame (the black) and screw the trays to it.
We have a discrete, and new, metal door but the inner handle is one that was in the house since the 1950’s.
On the outside there’s just a simple knob but it’s not linked to the lock. The handle works as intended but if we are not careful when pulling we end up with it on our hands.
I made a simple plate and kept the rod in place with an M4 screw threaded through it.
Looks like it came with the door:
Today I worked on the base mount for that bench. I chose a 20 degree slope (taken from that guide) as I found it comfortably and it’s a round number too.
I fumbled a bit with some pipes but the cuts and copes to build it properly are more demanding than the time I had, so I settled on some channel iron. The math is a lot easier, I just needed to offset one cut by (channel width) * tan(20°) or 2.6 cm.
I’m very pleased with how I managed to make this weld around the corner in one pass:
Just a small Sunday project.
Here at the Uni lab we have a nice articulated lamp that lacks a base. It’s been sitting on a corner for ages so I set to make a new clamp for it.
The frame is just a bit of T beam with a nut and some square tubes welded.
For the handle I used a bit of 3/8 threaded rod and a big washer I had lying around. In order to fix it I decided to make a hole along the axis and tap it to M3. After center punching the rod I screwed it to the drill press, using a center drill to align it. The plan was foiled when I tried to drill, as I left the base loose and it moved. But it’s good enough.
My initial idea was to use another nut and a locking pin behind the front washer but that used up a loot of the available space inside the clamp. After a bit of head scratching I ground a small taper and added a small washer to push the bigger one instead of a nut. I’m quite proud of how it turned out.