This is more or less a direct translation of the examples found at gstreamer/tests/examples/controller/*.c to their equivalents using the gi bindings for Gstreamer under Python. The documentation can be found here. Reading the source also helps a lot.
The basic premise is that you can attach a controller to almost any property of an object, set an interpolation function and give it pairs of (time, value) so they are smoothly changed. I’m using a pad as a target instead of an element just because it fits my immediate needs but it really can be any Element.
First you need to import Gstreamer and initialize it:
#!/usr/bin/python
import gi
import sys
from gi.repository import GObject
gi.require_version('Gst', '1.0')
from gi.repository import Gst
from gi.repository import GstController
from gi.repository import Gtk
from gi.repository import GLib
GObject.threads_init()
Gst.init(sys.argv)
Then create your elements. This is by no means the best way but lets me cut a bit on all the boilerplate.
p = Gst.parse_launch ("""videomixer name=mix ! videoconvert ! xvimagesink
videotestsrc pattern="snow" ! videoconvert ! mix.sink_0
videotestsrc ! videoconvert ! mix.sink_1
""")
m = p.get_by_name ("mix")
s0 = [pad for pad in m.pads if pad.name == 'sink_0'][0]
s0.set_property ("xpos", 100)
Here I created two test sources, one with bars and another with static that also has an horizontal offset. If we were to start the pipeline right now ( p.set_state (Gst.State.PLAYING) ) we would see something like this:
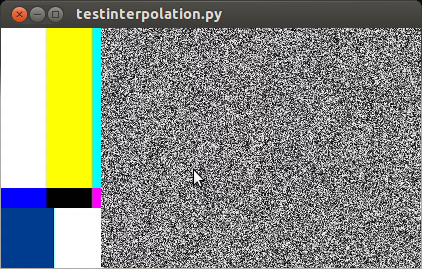
So far it works. Now I’d like to animate the alpha property of s0 (the sink pads of a videomixer have interesting properties like alpha, zorder, xpos and ypos). First we create a control source and set the interpolation mode:
cs = GstController.InterpolationControlSource()
cs.set_property('mode', GstController.InterpolationMode.LINEAR)
Then we create a control binding for the property we want to animate and add it to our element:
cb = GstController.DirectControlBinding.new(s0, 'alpha', cs)
s0.add_control_binding(cb)
It is worth noting that the same control source can be used with more than one control binding.
Now we just need to add a couple of points and play:
cs.set(0*Gst.SECOND, 1)
cs.set(4*Gst.SECOND, 0.5)
p.set_state (Gst.State.PLAYING)
If you are not running this from the interpreter remember to add GObject.MainLoop().run() , otherwise the script will end instead of keep playing. Here I’ve used absolute times, to animate in the middle of a playing state you need to get the current time and set the points accordingly, something like this will do most of the cases:
start = p.get_clock().get_time() # XXX: you better check for errors
end = start + endtime*Gst.SECOND
Avoiding too much bookkeeping
You can get the controller and control source of an element with:
control_binding = element.get_control_binding('property')
if control_binding:
control_source = control_binding.get_property('control_source')